25%: dat is het percentage gebruikt grondoppervlak aan effectieve opslag (= rekken of andere opslagtypes) in een gemiddeld magazijn. Je had meer in gedachten, niet? In deze post gaan we dieper in op het optimaal benutten (van het grondoppervlak) van beschikbare ruimte. Sommigen denken daarbij aan het volstouwen van het magazijn met rekken, werktafels, transportmiddelen, etc. Maar niets is minder waar, we ontdekken samen waar je moet op letten bij het indelen van je warehouse om tot een optimaal en slim resultaat te komen!
Voorstudie
De eerste fase van het indelen van je magazijn, of het nu gaat om een bestaande locatie herinrichten of beginnen vanaf nul, is de voorafgaande studie welke je doet (of laat doen). Zonder degelijke studie zal je nooit tot een goed resultaat komen, en dat hoeft geen ingewikkelde studie te zijn, gewoon even alle zaken op een rijtje.
Ervaring opdoen
Een efficiënt magazijn inrichten vanaf nul, zonder enige ervaring in de logistieke wereld, is heel moeilijk tot zelf praktisch onhaalbaar. Heb je geen ervaring, ga dan langs bij bedrijven uit de buurt die je kent of waar je denkt dat men op een gelijkaardige manier werkt. Alles wat je kan zien bij een ander, kan je meenemen (of net niet) naar je eigen magazijnomgeving. Met wat geluk krijg je tijdens zo’n bezoek ook nog eens heel wat waardevolle tips en tricks over hoe zij het hebben aangepakt en wat ze niet meer (of juist wel) zouden doen in de toekomst.
Heb je eerdere ervaring in een logistieke omgeving, schrijf dan neer wat er goed liep en wat er slecht was aan die specifieke omgeving, ook al was dit in een totaal andere sector. Dit zijn punten die je later in het proces kan gebruiken om niet dezelfde fout te maken of om je indeling beter te maken dan initieel voorzien.
Flows bepalen
Een eerste stap in het effectief indelen is het nadenken over de nodige flows in je magazijnomgeving. Denk daarbij aan:
- Inkomende goederen
- Tijdelijke wachtruimte
- Inkomende goederen
- Uitgaande goederen
- Opslag
- Picking
- Inpakken van orders
- Intern transport
- Afvalverwerking
- Bureelruimte
- Sanitair
Zorg ervoor dat je altijd uitgaat van ‘worst case’ scenario’s zodat je voldoende kan anticiperen waar nodig. Volgens het type product wat je zal stockeren, en de hoeveelheid mensen die in je magazijn rondlopen, zullen deze flows er anders gaan uitzien. Denk per onderdeel van je logistieke proces na welke stappen er nodig zijn, en wat je daarvoor allemaal nodig hebt aan ruimte en indeling.
Beperkt je daarbij niet enkel tot de essentiële zaken (zoals opslag en inpakken) maar denk ook aan randactiviteiten zoals afvalverwerking en veiligheidsmateriaal welke een plaats in je magazijn zullen innemen. Waarschijnlijk zal je ook een bureauruimte moeten voorzien waar er de nodige administratie kan gedaan worden.
Opslagtechnieken
Een belangrijk onderdeel van een magazijn is natuurlijk de opslag van goederen. Zoals aangehaald in de intro wordt gemiddeld zo’n 25% van het grondoppervlak gebruikt voor effectieve stockage. De rest van de ruimte zal gaan naar gangpaden, wachtruimte, inpaktafels, afvalstromen, etc…
Afhankelijk van welke types producten je wil stockeren, zullen er ook verschillende opslagtypes gebruikt worden, de lijst is eindeloos maar dit zijn enkele voorbeelden van veel gebruikte types:
- Palletrekken
- Draagarmstellingen
- Legbordstellingen
- Pickbakken
- Gerobotiseerde opslag (bvb Autostore)
- Verticale opslag (bvb Kardex)
Werkmiddelen
De beschikbare werkmiddelen in je magazijn zorgen voor een vlotte aaneenschakeling van de verschillende flows. Hoe raken de producten van punt A naar punt B? Hoe zullen de orders gepickt worden? Waar en hoe zullen de gepickte orders ingepakt worden? Wat met de klaargemaakte orders?
Al die werkmiddelen hebben plaats (tijdens of na gebruik) nodig, zorg dus dat deze ook aan bod komen op je plattegrond:
- Transpalletten (manueel of elektrisch: oplaadpunten nodig?)
- Heftrucks of stapelaars
- Rollenbanen
- Pickkarren
- Pickrobots (goods to person, shelf to person, …)
- Inpaktafels
- Veiligheidselementen (brandblussers, EHBO, …)
- Oplaadstations
- Computers en printers
Ademruimte
Het klinkt misschien vreemd, maar ademruimte is topprioriteit bij het uittekenen van je magazijn. Zonder die noodzakelijke open ruimte, zal er nooit een efficiënte flow ontstaan. De nodige vrije ruimte zorgt voor overzicht en rust in je magazijn, twee heel belangrijke elementen tijdens de dagelijkse bedrijfsvoering. Wanneer alles op een hoop staat, raken medewerkers al gestresseerd door er alleen maar naar te kijken, laat staan in zo’n omgeving te moeten werken. Die open ruimte kost je inderdaad veel geld, maar zal je op het einde van de rit nog veel meer geld besparen op allerlei vlakken.
Slimme magazijnindeling
Na de voorstudie, die kan ofwel enkele uren ofwel enkel dagen/weken in beslag nemen, is het tijd voor het echte werk. Alle theorie stilaan omzetten in de praktijk. Maar hoe doe je dat nu precies?
Plattegrond schets
Neem de plattegrond van je magazijn er alvast bij, zorg dat enkel de muren zijn ingevuld, de rest is idealiter blanco. Met deze plattegrond kunnen we aan de slag om de lijnen van ons magazijn verder uit te tekenen. Gebruik hiervoor een gratis programma als Sketchup of ga aan de slag met pen en papier (zorg in dat geval eventueel voor een afdruk op minimaal A3 formaat, dat werkt niet iets handiger).
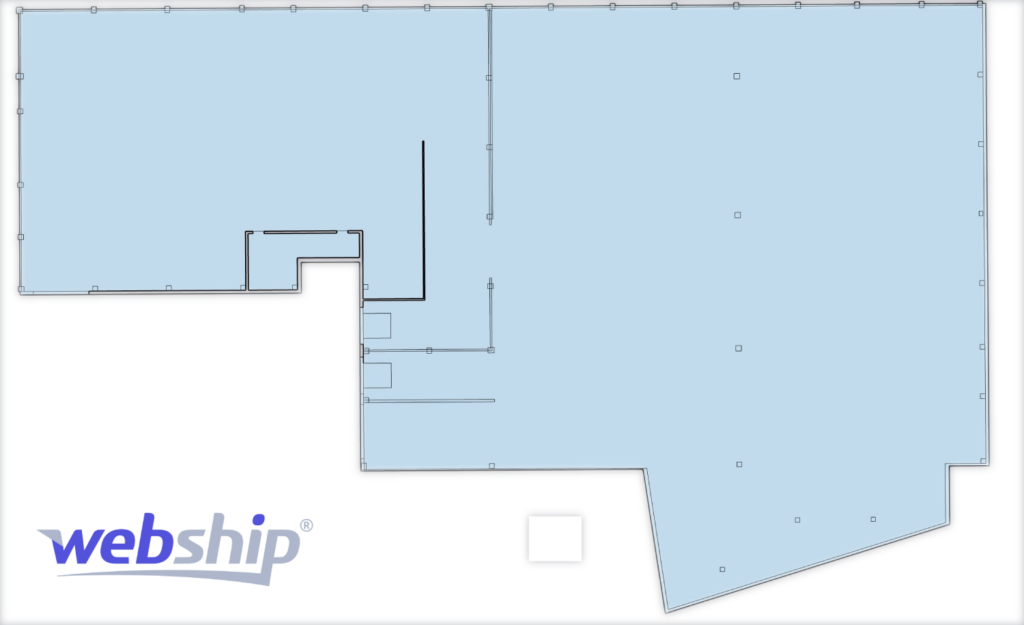
Zones bepalen
Probeer de belangrijkste flows die in je magazijn zullen plaatsvinden, in zones op te delen. Die zones kan je nu in grote lijnen aanduiden op de plattegrond van je magazijn. Zorg natuurlijk voor een logische indeling: teken de inbound zone op de plaats waar je goederen fysiek het magazijn zullen binnen komen, zet de opslagzone ongeveer waar de verschillende opslagtypes zullen komen, etc… Je hoeft nog niet in detail te gaan, geen rekening te houden met gangpaden, etc… het gaat in deze fase enkele om de ruwe contouren.
Type goederen en omloopsnelheid
De opslagzone(s) kan je verder onderverdelen volgens type opslag. Dit zal voornamelijk gebeuren op type goederen (groot, klein, voeding, BIO, FIFO, FEFO, …) en op de omloopsnelheid (A, B of C goederen). Ongeveer 20% van de producten zullen A (5%) en B (15%) zijn, dit zijn producten die snel omlopen en welke je dus dicht bij de inpakzone wil houden. De overige 80% zijn C producten die je wat verder in je magazijn kan stockeren.
Zorg ervoor dat je medewerkers zo min mogelijk afstand moeten afleggen op een dag, elke meter die ze per dag uitsparen, is op het einde van het jaar een grote afstand welke hen niet fysiek belast en welke tijd uitspaart voor andere zaken.
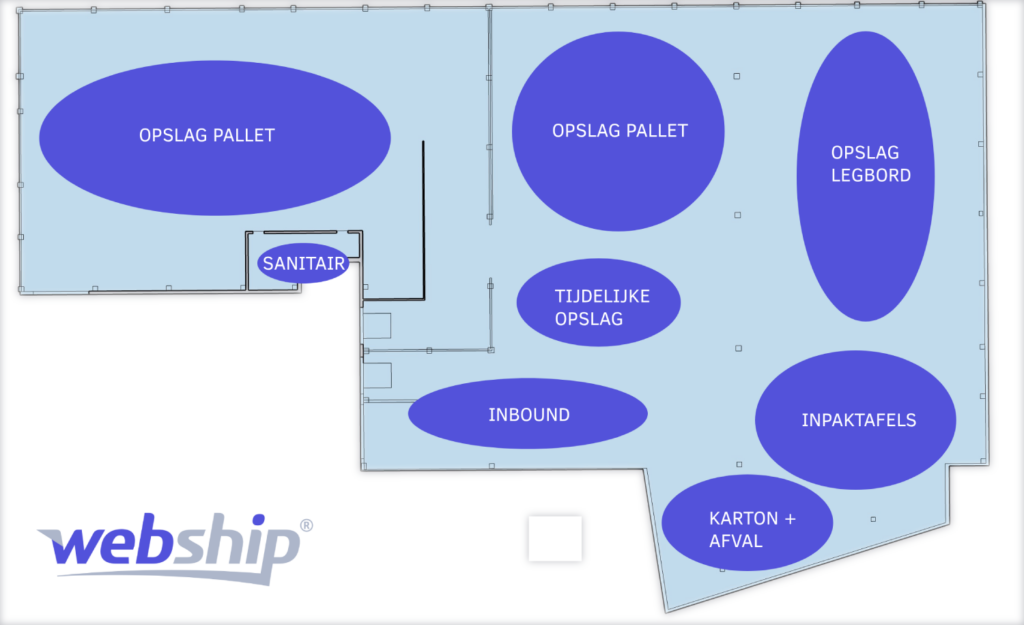
Dynamische locaties
Geef je producten geen vaste locaties maar werk met een dynamisch systeem. Afhankelijk van de product eigenschappen (zie hierboven) kan je bepaalde voorraad toekennen aan bepaalde plaatsen in je magazijn. Komt die plaats later vrij, dan kan je die gebruiken voor producten met dezelfde eigenschappen (bvb A producten) maar daarom niet persé dezelfde producten. Door op deze manier te werken zal je je opslagsysteem efficiënt gebruiken en zal je ook fouten reduceren. Je dient hiervoor wel je locaties van een logische nummering te voorzien.
Gedetailleerde uitwerking
Eénmaal je alles zones vasthebt op je plattegrond, is het zaak om dit steeds verder en verder uit te werken tot je een op de centimeter nauwkeurige bepaling hebt van wat er waar zal komen. Van het grootste palletrek tot de kleinste vuilnisemmer en alles daartussen.
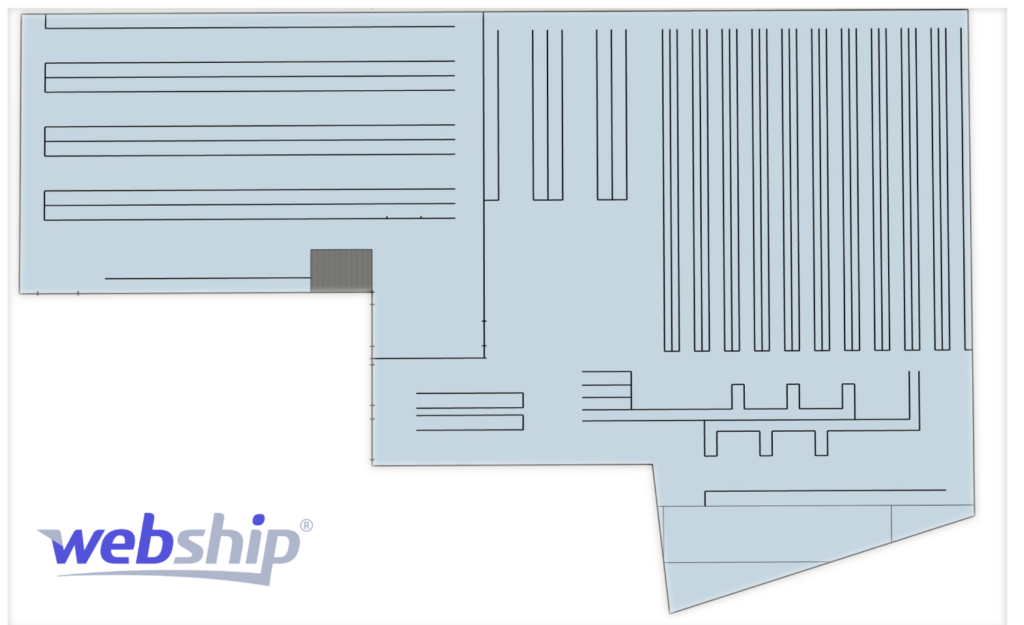
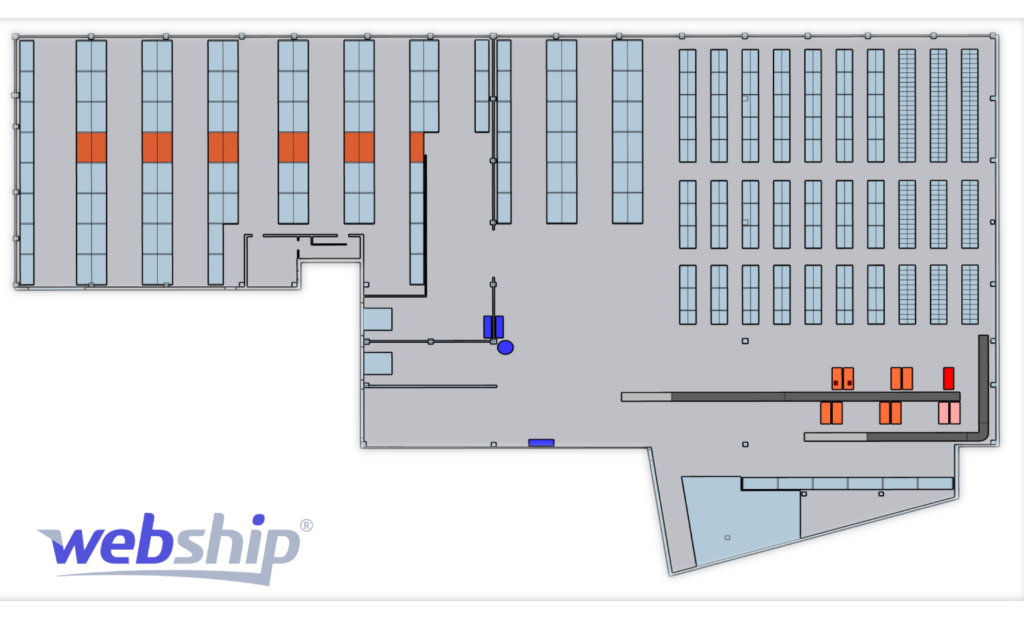
We kunnen het niet genoeg benadrukken, maar voorzien voldoende ruimte. Neem liever wat teveel speling dan te weinig, het is later altijd prettiger om meer ruimte te hebben dan voorzien, dan voortdurend in een te krappe omgeving te moeten werken.
Probeer niet ‘slim’ te zijn door in te boeten op gangpaden, om zo meer rekken te kunnen plaatsen. Bekijk wat de specificaties zijn van je werkmiddelen (bvb stapelaar) en wat de minimum aangeraden gangbreedtes zijn. Zorg ervoor dat je medewerkers ook niet op elkaar moeten wachten in de gangpaden maar maak het mogelijk elkaar te kruisen.
Nu je alles in detail hebt uitgetekend, kan je ook nadenken over logische locatie nummering en zone-aanduiding. Kies je ervoor om met het huisnummer systeem te werken (links oneven, rechts even nummer), het ‘slang principe’ (op het einde van een gangpad, begint de nummering in de volgende gang terug vanaf 0), of nog een andere benadering?
Een handige magazijnsoftware kan op basis van je zones en nummering de pickroute bepalen, belangrijk om dus niet in elkaars weg te lopen. Dat geldt trouwens ook voor het wegzetten van de inkomende goederen, probeer te vermijden dat die flow in aanraking komt met de picking flow, al is dat niet altijd evident.
Fysieke uitwerking
Nadat je alles tot in het kleinste detail hebt uitgewerkt, is het dan eindelijk zover. Eigenlijk de makkelijkste stap in heel het proces, terwijl de voorgaande stappen vooral een aaneenschakeling van trial en error was (schrappen, opnieuw intekenen, terug schrappen, nachtje over slapen, etc…) zal er in deze fase nog weinig marge zijn voor aanpassing. Eenmaal je leveranciers vast liggen, is het kwestie van wachten en/of doen om de uitgetekende plannen tot uitvoering te brengen.
Implementatie
Tijdens de eigenlijke implementatie belet niets je natuurlijk om links en rechts nog kleine aanpassingen te doen op basis van wat je ziet verschijnen: die rekken mochten toch iets meer naar links, of komen toch net iets te ver, … op zich geen ramp, de theorie zal nooit helemaal stroken met de praktijk. Probeer je echter zoveel mogelijk aan het vooropgestelde plan te houden, tenzij je daar natuurlijk echt goede redenen voor hebt.
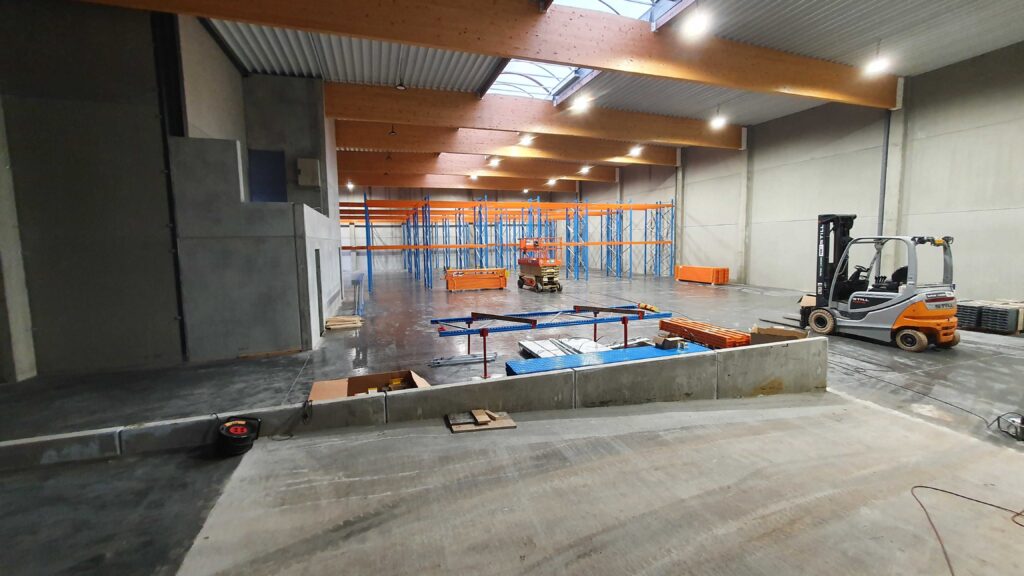
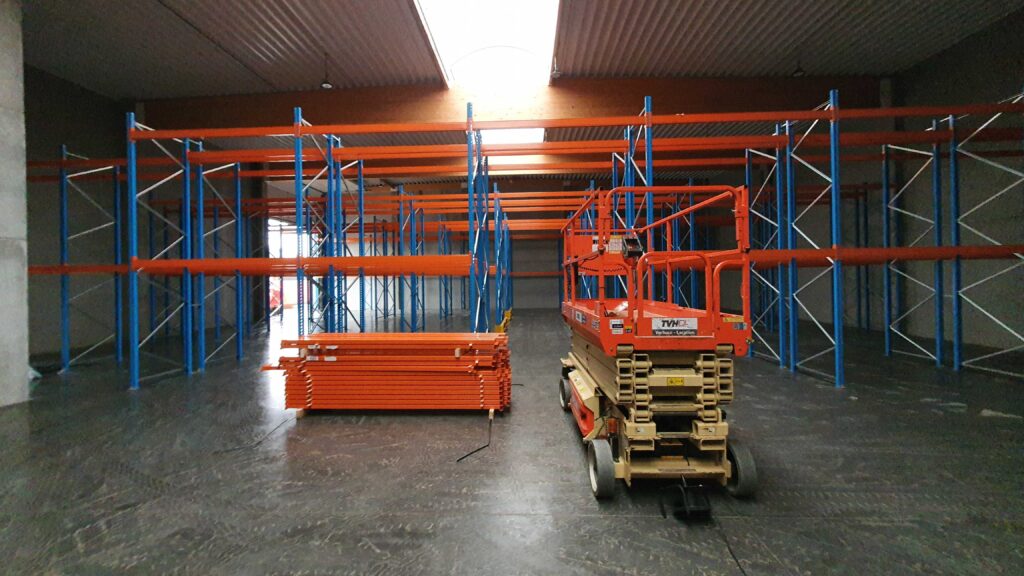
Ingebruikname
Nadat alles werd opgeleverd, is het dan ook snel tijd voor de werkelijke ingebruikname. Waarschijnlijk wil je je fysieke omgeving wel omzetten in een virtuele door middel van een Warehouse Management System te gebruiken. Daarin kan je je opgebouwde structuur omzetten in een bruikbare software (zones, locatienummering, …) om dan echt te kunnen starten met het inboeken van de eerste producten en verwerken van de binnenkomende bestellingen.
Na verloop van tijd zal je ongetwijfeld enkele aanpassingen willen doen aan de bestaande infrastructuur. Voorzie daarom genoeg ‘witruimte’ rond de cruciale punten in je originele plannen om dan toch hier en daar wat wijzigingen te kunnen doen.
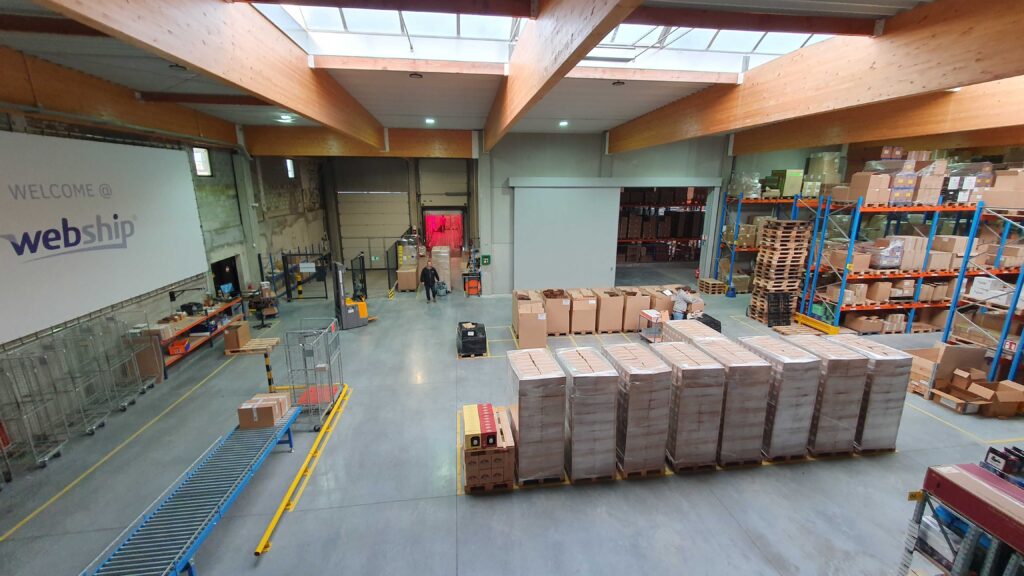
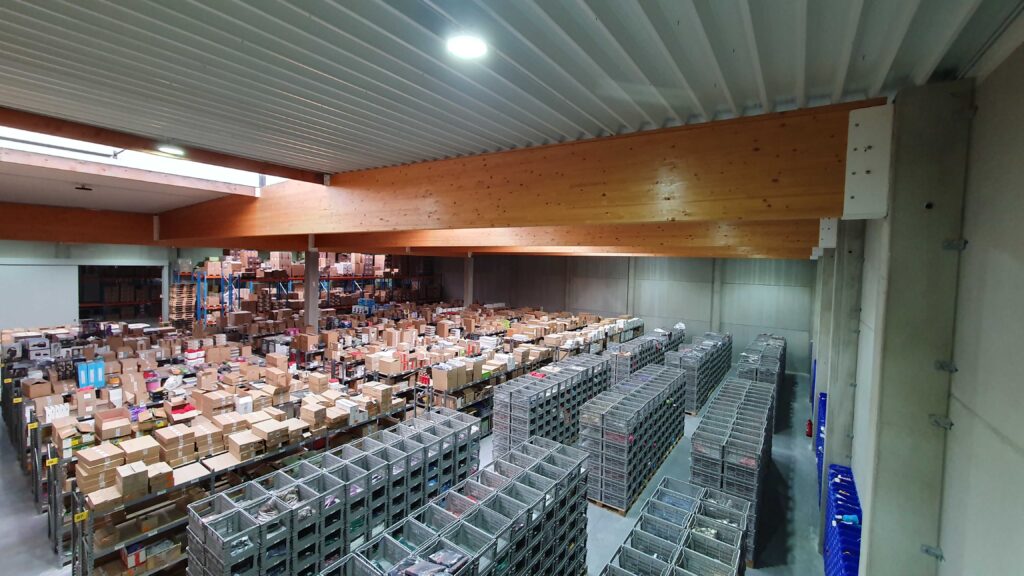
Conclusie
Er komt dus heel wat kijken bij het efficiënt indelen van je magazijn. We bespraken enkele belangrijke zaken maar nog lang niet alles. Zo zouden we het ook nog kunnen hebben over het intern transport (bvb gebruik van rollenbanen) of het indelen en uitrusten van je inpaktafels. We houden het echter bij de grote lijnen, en kunnen concluderen:
- Denk vooraf voldoende na over je logistieke flows
- Maak een ruwe schets en werk deze stap voor stap verder uit
- Voorzie voldoende ademruimte
- Maak gebruik van een degelijke magazijn software
- Stuur bij waar nodig